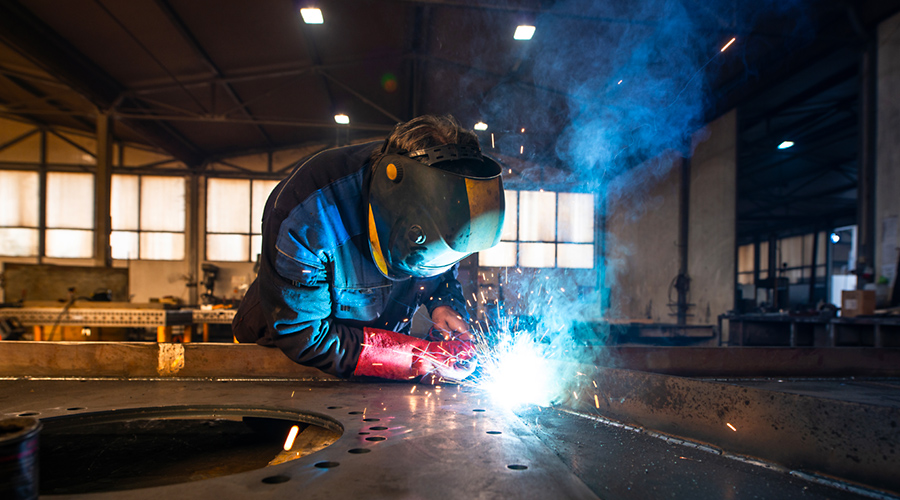
Stainless Steel Welding Types
Stainless steel is the name commonly used to refer to steels that resist various types of corrosion. Basically, stainless steel must contain at least 10.5% chromium by weight up to values in the order of 30%.
It was found that by adding chromium to steel, the steel did not corrode under normal conditions. And therefore they are not deteriorated by the action of oxidation, either produced by contact with water, or by that generated by the air itself.
This essential characteristic makes these steels widely used in industry. Typically in the chemical, food, architectural, nuclear, etc. sectors. It can be said that all the key sectors of industry make use of this material and therefore of stainless welding.
There are three types of welding which are the most commonly used on stainless steels.
- Arc welding or SMAW.
- TIG welding.
- MIG/MAG welding.
1 – Arc Welding or SMAW
Shielded Metal Arc Welding (SMAW) is characterised by the maintenance and creation of an electric arc between the base material to be welded and a metal rod called an electrode.
During the process the electrode is a coated wire, in which the welder controls the process manually over the length and direction of the arc that is established between the base metal (or piece to be welded) and the end of the electrode.
Some of the advantages of SMAW welding are:
- Simple, portable and low-cost equipment.
- Applicable to a wide variety of metals, welding positions and electrodes.
- Relatively high metal deposition rates.
- Suitable for outdoor applications.

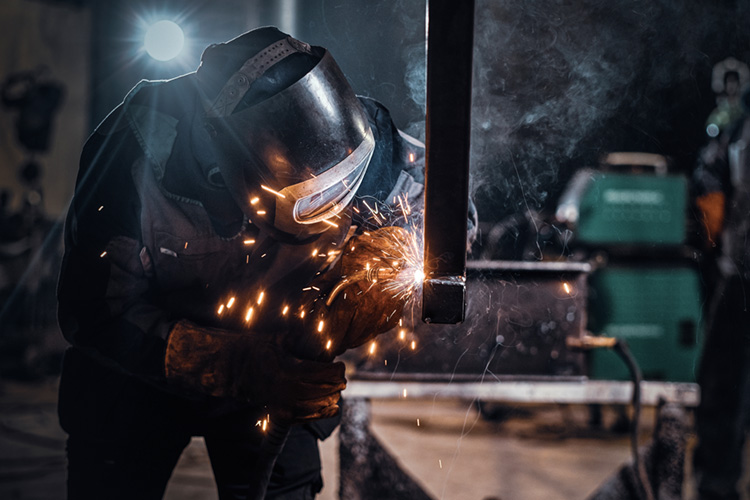
2 – TIG Welding
In this type of welding (Tungsten Inert Gas) the electric arc is generated between the base metal and a non-consumable tungsten electrode, under a protective atmosphere generated by the inert gas, which is normally argon.
The TIG welding process forms high quality, slag-free beads by using non-consumable electrodes without coating or spatter. This makes it used for high responsibility welding on stainless steel, where high quality welds are of paramount importance.
In addition to its use in critical welding, it is also widely used in thin parts, approximately up to 6 mm thick, as welding parts thicker than 6 or 7 mm would not be economical. For thicker parts, submerged arc welding is often used.
Some of the advantages of TIG welding:
- No slag in the seam.
- Can be used in any position of the weld.
- Does not generate any spatter around the bead.
- It does not affect the chemical composition and properties of the base metal used in the weld.
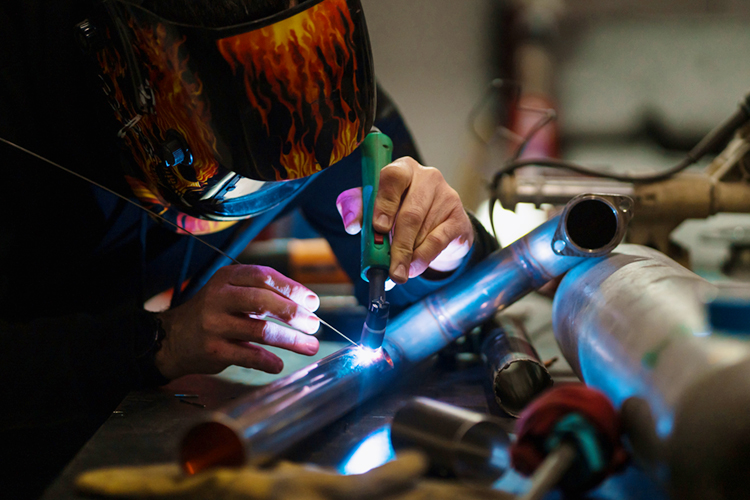
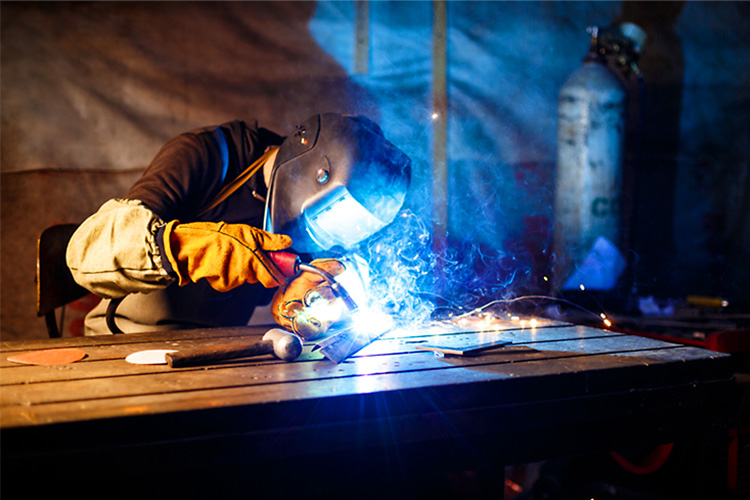
3 – MIG/ MAG Welding
Both MIG (Metal Inert Gas) and MAG (Metal Active Gas) welding are used to achieve the gaseous protection of an inert gas, establishing an electric arc between a consumable electrode (presented in the form of bare wire), and the base metal or piece to be welded.
This type of welding is ideal for stainless steel, both the weld and the arc will be protected from atmospheric air by the action of a gaseous envelope.
Some of the advantages MIG/ MAG welding:
- Allows higher welding speeds.
- Allows for ease of process automation.
- Provides very good transfer of filler metal through the arc.
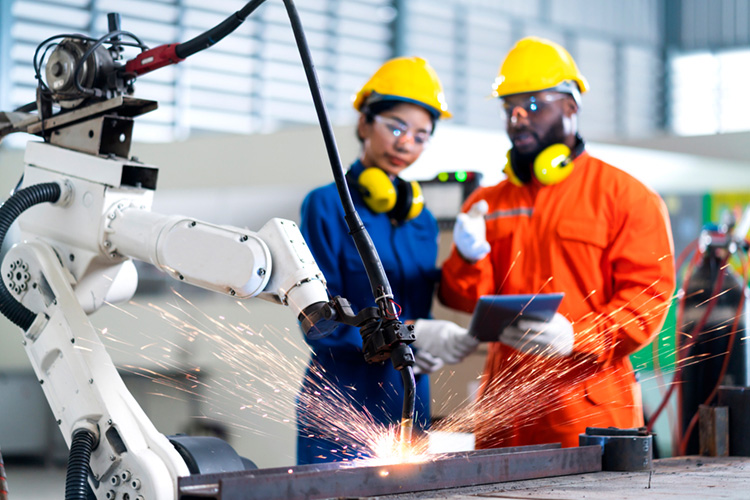
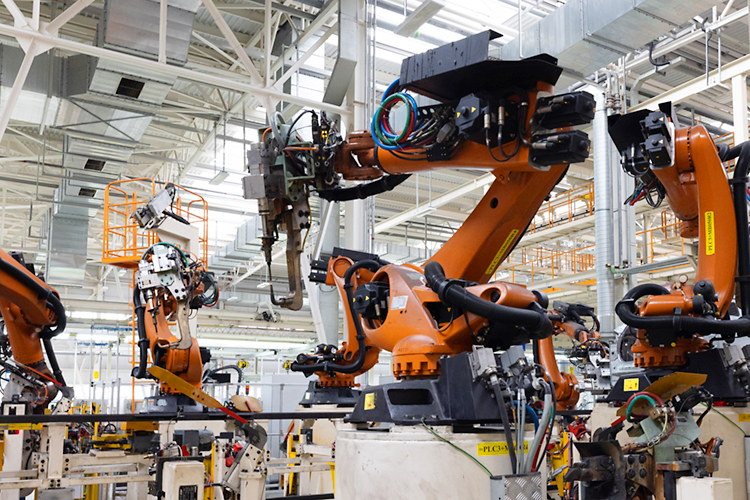
Which Stainless Steel Welding Method is Best?
The answer is not that simple. It depends on the result you are trying to achieve. Each of these processes will produce a slightly different result. To find the best welding process for your project, you should consider the following factors: the skill level of the welder, the aesthetics of the final part including the appearance of the bead, the thickness of the metal plus the cost and time factors of the project. If artistry is paramount, then the finesse of TIG welding may be a good fit, but if speed and efficiency are a priority, then MIG welding may be a better process.
As always, for both the choice of steel and the right welding equipment, our Technical Department will advise you in finding the best solution for your needs and the characteristics of the project.